4.跟刀架跟刀行駛時,車刀與後面的支撐頭距離盡量近些,車刀刀尖高度高於中心0.2mm,粗車第一刀時一般切削深度較大,為防止跟刀尺寸忽大忽小,操作者需隨時手動調節支撐頭壓力,另外操作者要用外卡鉗隨時測量工件外徑,中途不停車,做一些進退刀微調節,跟刀架第一刀目的就是去掉黑皮和彎曲量,尺寸允許有較大變化,後面第二刀/第三刀就會平穩下來,彎曲度會逐漸校正;(5)跟刀接觸壓力過小或不接觸,就不起作用,不能提高零件剛度;若壓力過大,零件壓向車刀,切削深度增加,車出的直徑就小,繼續移動後,支承塊支承在小直徑外圓處,支承塊與工件脫離,切削力使工件向外讓開,車出的直徑會變大,到跟刀架跟到大直徑圓上,又把工件壓向車刀,使車出的直徑變小,這樣反覆變化,會把工件車成「竹節」形;此時,要退刀,可減慢一檔速度加工,以粗加工時常見;(6)長軸加工,跟刀架使用是關鍵,操作者在加工中要保持較高注意力,不可分心,右手要隨時觸摸支撐頭手輪,輕微調節壓力,並輕微感受尾座頂緊力,適當調節,粗車時會緊張些,操作者要不斷觀察調節各方壓力,半精車後變形微小,調節基本上就少了;經過反覆觸摸感受手輪壓力,跟刀架是很好掌握的;三爪跟刀架可以使用較高的速度切削;一夾一頂上跟刀架,不允許調頭接刀車削;
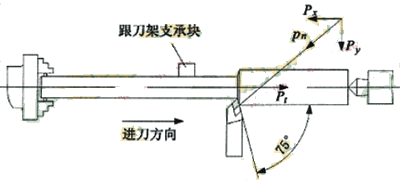
細長軸反向進給加工,降低振動
採用反向進給車削:反向進給就是在床頭工件位置,用尖刀車出空位,能安裝跟刀架,然後刀具從床頭到床尾方向作切削運動。常規的切削方向使尾座的頂緊軸向力與切削軸向力Px方向一致,加劇了細長軸的彎曲。若反向進給,其軸向分力對工件會產生拉力,使工件已加工部分軸向拉伸,與工件變熱伸長方向一致,反向相對於正向進給,平穩性和抗振性還要好;如配合彈:性頂尖可顯著降低變形;

合理選用車刀角度,此是90度刀
合理選擇車刀幾何形狀:車削講究「三分技巧七分刀」,合理選擇刀具角度是實現穩定切削的關鍵:1.前角r0。 隨著前角的增大,振動會隨之下降,但在切削速度較高的範圍內,前角對振動的影響將減弱;由於細長軸車削速度一般不會太高,故而粗加工中取r0=20°,精車時取r0=25°;2.主偏角Kr。主偏角Kr對振動強度有影響,當切削深度和進給量不變時,隨著主偏角的增大,振幅將逐漸減小,這是因為徑向切削力減小了,同時實際切削寬度aw將減小;粗車削長軸時刀具取Kr=75~80°,精車時取Kr=85~90°來進行切削,可避免或減小振動。在不影響刀具強度的情況下應盡量增大主偏角,可以用主偏角Kr=90°的刀具,裝刀時可裝夾成85°~88°角度,效果一樣理想;3.後角a0。一般後角對切削穩定性無大影響,但當後角減小到2~3°時,振動會有明顯減弱,現實中後刀面有一定程度的磨損後,也會有顯著的減振作用。4.刀具圓弧半徑rs。刀尖圓弧半徑rs增大時,徑向分力也隨之增大,為避免自振,rs越小越好。但隨rs的減小,將會使刀具壽命降低,同時不利於表面粗糙度的改善;故加工中,斷屑槽寬度應取R1.5~3,刀尖圓弧r=0.5;(5)刀具應用中,跟刀加工要切實保證斷屑,以利排屑順暢,長屑會嚴重損傷跟刀架;刀具應保持銳利以減小刀具與工件的摩擦,鋒利之時也要兼容一定刀具強度,切削速度不可過快,合金刀頭打了不僅會使工件瞬間輕微彎曲,合金頭鑲進工件表面會造成二次刀具傷害;

切削用量的三要素圖
合理選擇切削用量可降低變形:(1)切削深度(t) 在工藝系統剛度確定的前提下,隨切削深度的增大,車削時產生的切削力、切削熱也隨之增大,那麼長軸的受力、受熱變形也增大。應盡量減少切削深度,筆者建議:粗車雙邊6mm內,半精車雙邊2~3mm內,精車雙邊0.5~1mm內;(2)進給量(f) 進給量增大會使切削厚度增加,切削力增大。從提高切削效率的角度來看,增大進給量比增大切削深度有利,但前提工件需有足夠的剛性和強度;長軸只適合小進給量,粗車0.1mm,精車0.03~0.05mm左右; (3)切削速度(v) 提高切削速度有利於降低切削力,隨著切削速度的增大,切削溫度提高,刀具與工件之間的摩擦力減小,細長軸的受力變形會減小。但切削速度過高,離心力會加大,破壞切削的平穩性,所以切削速度應控制在一個中性範圍;如何衡量主要看跟刀架跟刀效果是否有震動,震動就降一級處理,如跟刀架平穩切削無震動,可取較高轉速值;較高轉速利於合金刀切削;

粗精車步驟要細分,減少變形
合理選擇粗精車順序來消除變形:首先進行粗車,切削時如跟刀無問題,中途不能停車,車刀有正常磨損,操作者要用外卡鉗(憑經驗)不時測量切削出來的軸徑變化,同時應適當微量進刀,補償車刀的磨損量,粗車後表面粗糙度可達Ra12.5;如出現竹節、麻花、振紋現象時,要退刀,可減慢一檔速度加工;注意:「粗車第一刀一定要切淨黑皮」。因表皮的硬度不一,且有彎曲,粗車後的軸一定有彎曲變形;所以精車/半精車要留夠余量;其次半精車:換上精車刀,換上優一級數的跟刀架支撐爪,重複粗車時的各項程序進行切削,半精車後軸通常不會彎曲變形,表面粗糙度可達Ra6.3左右;為安全起見,半精車可以分兩次/三次加工;如是長軸絲桿,半精外圓分兩次,先粗車挑螺紋,可先用白鋼切刀切出螺紋底徑,留余量,再分別粗車梯形螺紋兩側面,留余量;再進行二次外圓半精車; 最後精車:如採用低速精車,中途可隨意停車測量工件尺寸變化,也可在切削中作微量補償進給,便於工件尺寸控制,但不便提高表面質量;生產中多採用紅硬性、耐磨性都很好的YT15刀片,進行較高速切削,尺寸精度可達6級,表面粗糙度可達Ra1.6以上;如車床加裝電動拋光千葉輪進行拋光處理,表面粗糙度可達Ra0.6以上;
兄弟,說實話如果你以上幾點做到了,管你數控車床還是普通車床皆不在話下。只是細節太多,但禁不住實用啊! 你若喜歡請收藏。